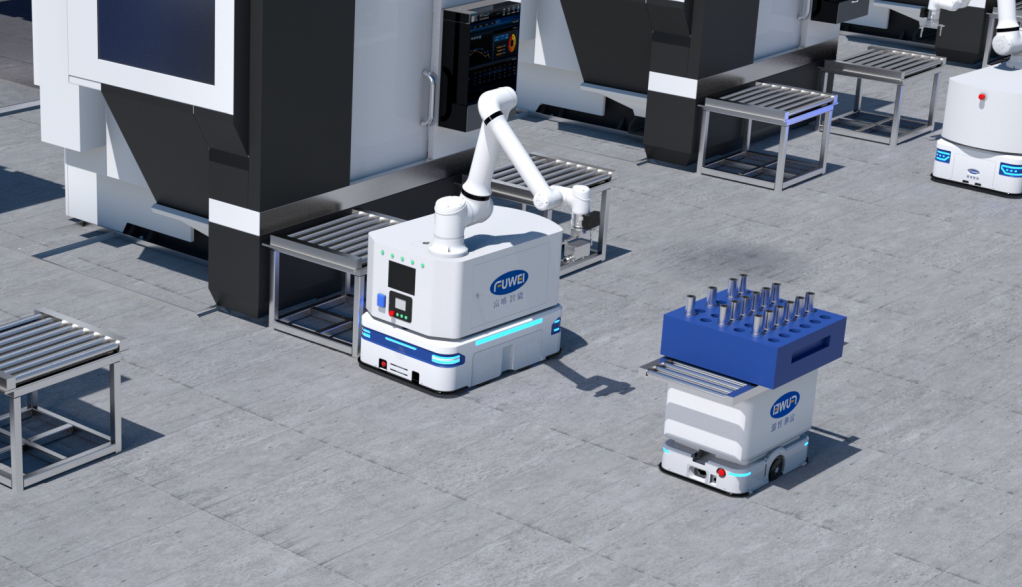
富唯智能凭借自主研发的协作机器人搭载3D视觉精度解决方案,为3C电子、汽车制造、精密装配等领域注入颠覆性变革力量,助力企业实现从“经验驱动”到“数据驱动”的智能跃迁。
一、精度革命:从“人眼极限”到“机器慧眼”的跨越
传统工业场景中,人工质检受限于视觉疲劳与经验偏差,即使顶尖技师也难以稳定识别0.1mm级的缺陷。而协作机器人搭载3D视觉精度系统,通过“高帧率3D相机+AI算法引擎+自适应力控”的三维协同,将检测精度提升至±0.03mm,相当于人类头发丝直径的1/3。
以3C行业为例,手机中框的全尺寸检测需在2秒内完成200+项参数扫描,传统2D视觉因无法捕捉曲面特征,良品率长期徘徊在95%以下。而富唯智能方案通过3D点云重建与深度学习模型,可精准识别亚克力、金属、玻璃等材质的微米级划痕与形变,将缺陷漏检率降至0.005%。某头部手机厂商引入后,单线年节省返工成本超800万元。
二、技术内核:四大硬核能力定义工业新标准
协作机器人搭载3D视觉精度的竞争力,源于富唯智能独创的“感知-决策-执行”闭环架构:
1.超高速扫描:采用TOF+结构光融合技术,每秒生成30万点云数据,动态捕捉高速产线上的微小目标8;
AI自适应优化:内置自研算法库,可针对反光、透明、曲面等复杂材质实时调整曝光与滤波参数,避免误检漏检12;
力控柔顺协作:六维力传感器与阻抗控制算法结合,实现“视觉定位+柔性装配”一体化,装配压力误差≤0.1N;
边缘智能决策:搭载国产高性能边缘计算模块,推理延迟压缩至5ms,支持产线实时闭环优化。
三、场景赋能:从精密制造到柔性生产的全链路突破
协作机器人搭载3D视觉精度已深度渗透工业核心场景:
3C电子:手机电池仓异物检测中,系统可区分0.05mm金属碎屑与同色背景干扰,误判率降低90%;
汽车制造:针对新能源电池模组的插针装配,通过3D视觉引导+力反馈修正,将插接成功率从82%提升至99.9%;
半导体封装:晶圆搬运过程中,动态补偿机械振动导致的微米级偏移,定位精度稳定在±5μm;
医药包装:药瓶液位检测精度达±0.1ml,同步识别标签印刷缺陷,实现100%全检替代抽检。
更值得关注的是其柔性换型能力——通过预设工艺参数库,5分钟内切换检测/装配模式,支持最小批量1件的定制化生产,彻底打破“量产即正义”的旧范式。
精度,是工业智造的终极命题。协作机器人搭载3D视觉精度技术,不仅重新定义了生产标准,更让企业拥有了对抗不确定性的核心武器。面对全球化竞争与个性化需求的双重挑战,唯有以精度为刃,方能破局而立。