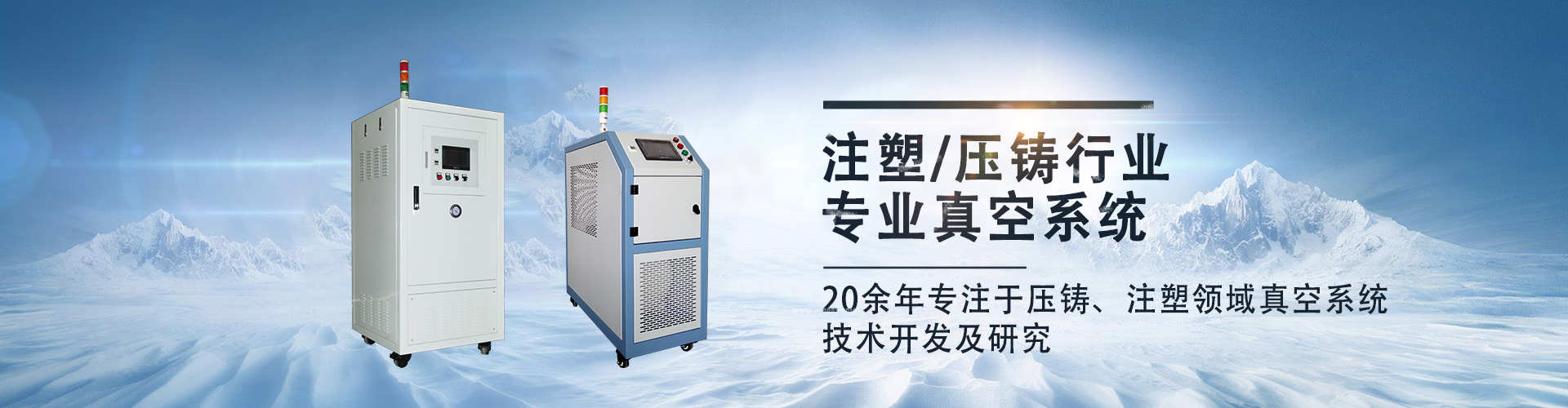
压铸作为一种高效的金属成型工艺,在现代制造业中占据重要地位。通过高压将液态或半液态金属快速压入模具型腔,能够生产出尺寸精确、表面质量高且复杂程度多样的零部件。然而,传统压铸过程中,型腔中的气体难以完全排出,易在铸件内部形成气孔、疏松等缺陷,严重影响铸件的力学性能和质量稳定性。为解决这一难题,真空机工艺被引入压铸领域,通过抽取型腔中的气体,显著降低气体含量,提升铸件品质。深入探讨压铸与真空机工艺的协同作用,对于优化压铸生产、拓展应用领域具有重要意义。
1、压铸工艺基础
压铸过程始于将金属材料(如铝合金、锌合金等)在熔炉中加热至液态。借助压铸机的压射系统,以极高的压力和速度将液态金属注入模具型腔。模具通常由定模和动模两部分组成,合模后形成与铸件形状相符的封闭空间。在高压作用下,液态金属迅速填充型腔的各个角落,并在模具冷却系统的作用下快速凝固成型。
压铸工艺具有诸多优势,生产效率极高,能实现短时间内的大量生产,适合大规模工业化生产需求。且所得铸件尺寸精度高,公差范围可控制在极小范围内,表面粗糙度低,减少了后续加工工序。但不可忽视的是,由于金属液高速充型,型腔中的空气难以完全排出,会卷入金属液中形成气孔。这些气孔不仅降低铸件的密度,还会成为应力集中点,在受力时可能引发裂纹扩展,降低铸件的强度、韧性和疲劳性能 。
2.真空机工艺原理与作用
(一)原理
真空机工艺的核心原理是在压铸过程中,通过真空系统将模具型腔中的气体抽出,降低型腔内的气压。在开始压铸前,启动真空机,利用真空泵的抽吸作用,使模具型腔与外界形成压力差,从而将型腔中的空气、水汽以及其他挥发性气体排出。当型腔内达到预定的真空度后,再进行液态金属的压射充型。此时,由于型腔内气体含量大幅减少,金属液在填充过程中卷入气体的几率显著降低。
(二)作用
减少气孔缺陷:显著降低铸件内部气孔的数量和尺寸,使铸件更加致密。这对于承受高压、高载荷的零部件尤为重要,如汽车发动机缸体、航空航天结构件等,可有效提高其力学性能和可靠性。
提升力学性能:减少气孔后,铸件的强度、韧性、疲劳寿命等力学性能指标得到显著提升。例如,铝合金压铸件经真空压铸后,其抗拉强度可提高10%-30%,疲劳寿命可延长数倍。
改善表面质量:减少因气体卷入导致的表面缺陷,如气泡、麻点等,使铸件表面更加光滑平整,提高产品的外观质量和表面光洁度,减少后续表面处理工序的成本。
3.压铸与真空机工艺协同关键技术要点
(一)真空系统设计
真空泵选型:根据压铸机的规格、模具型腔体积以及所需的真空度要求,选择合适抽气速率和极限真空度的真空泵。例如,对于大型压铸机和较大型腔的模具,需配备抽气速率高的罗茨真空泵与旋片真空泵组合系统,以快速达到所需真空度。
真空管路布局:合理设计真空管路,确保管路短而直,减少弯头和接头数量,降低气体流动阻力。同时,要保证管路的密封性,防止外界空气泄漏进入型腔,影响真空效果。
(二)模具设计与制造
排气槽设计:在模具型腔的适当位置开设排气槽,排气槽的深度和宽度需根据铸件的材质、厚度和形状进行优化设计。一般来说,排气槽深度在0.05 - 0.2mm之间,宽度根据型腔大小在5 - 20mm不等。排气槽应与真空系统相连通,使气体能够顺利排出。
模具密封:提高模具的密封性能,防止金属液在压射过程中从分型面、滑块等部位泄漏。采用优质的密封材料和合理的密封结构设计,如在分型面设置密封槽,安装橡胶密封条等。
(三)压铸工艺参数匹配
压射速度与真空开启时机:精确控制压射速度与真空开启时机的匹配关系。在真空系统达到预定真空度后,适时启动压射动作,且压射速度要适中,既要保证金属液能够快速填充型腔,又不能因速度过快导致气体再次卷入。例如,对于薄壁铝合金压铸件,可在真空度达到95%以上时启动压射,压射速度控制在3 - 5m/s。
压铸压力与保压时间:在真空压铸过程中,压铸压力和保压时间也需要进行优化调整。由于型腔内气体减少,金属液的流动性和填充性能有所改变,适当提高压铸压力和延长保压时间,有助于提高铸件的致密度和尺寸精度。
4.应用案例分析
在汽车行业中,某汽车制造公司采用真空压铸工艺生产铝合金发动机缸体。传统压铸工艺生产的缸体内部存在较多气孔,在进行压力测试时,部分缸体出现渗漏现象,废品率较高。采用真空压铸工艺后,通过优化真空系统和压铸工艺参数,缸体内部气孔率大幅降低,废品率降低了50%以上。经检测,真空压铸生产的缸体抗拉强度提高了15%,疲劳寿命延长了2倍,有效提升了发动机的性能和可靠性。
在航空航天领域,某航空零部件制造商使用真空压铸工艺制造钛合金结构件。由于航空航天零部件对质量和性能要求极高,传统压铸工艺无法满足要求。采用真空压铸工艺后,成功解决了气孔缺陷问题,生产出的结构件质量稳定,满足了航空航天领域对零部件高强度、高可靠性的严格要求。