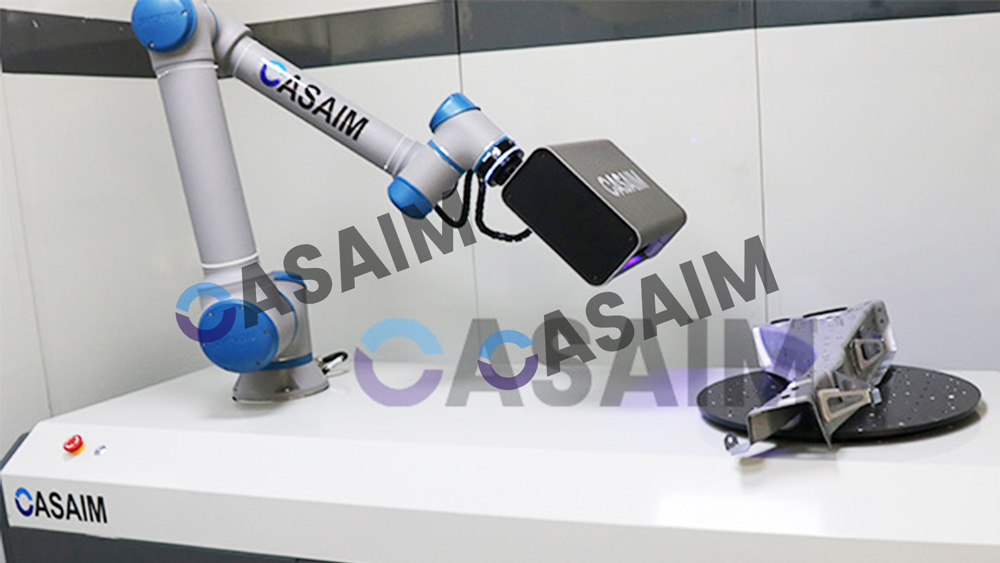
航空发动机中,涡轮叶片传统精密铸造需经历模具开发、蜡模成型、陶瓷壳制作等多道工序,耗时长达3个月,且成品率不足60%。某国际航空制造商采用 3D打印工艺后,成功将叶片交付周期压缩至72小时,合格率跃升至98%——这场效率革命的背后,是3D打印技术对极限制造的重新定义。
技术解构:什么是工业级3D打印?
3D打印(增材制造)通过逐层堆叠材料构建三维实体,其核心工艺技术包括:
主流 3D 打印技术:
►熔融堆积成型(FDM)
材料: ABS、PC、尼龙、 ABS 防静电材料、 PEEK 等工程塑料
►激光固化成型(SLA)
材料:光敏树脂(透明、黑色、白色、绿色)
►多射流熔融成型( MJF)
材料: PA12 粉末
►选择性激光烧结成型(SLS)
材料:尼龙粉、陶瓷与粘结剂的混合粉、金属与粘结剂的混合粉等
►选区激光熔化成型(SLM)
材料:铝合金粉末、纯钛/钛合金粉末、镍基合金粉末、不锈钢粉末等
例如用1070nm激光熔化金属粉末,适合制造耐1300℃高温的镍基合金叶片。
喷墨式光固化(Polyjet )
材料:树脂(类橡胶、透明、生物相容性材料、全彩制作等)
传统制造瓶颈:
1. 复杂结构受限:300个微孔的气膜冷却结构,传统工艺合格率仅30%;
2. 材料浪费严重:高温合金单价超¥2000/kg,铸造过程损耗达80%;
3. 迭代周期漫长:新机型叶片设计验证需6-8个月,延误研发进度。
3D打印解决方案:一体化成型:GE航空LEAP发动机燃油喷嘴,将20个零件整合为1个,减重25%,耐久性提升5倍;
材料利用率95%:未熔化的金属粉末可循环使用,单件成本降低40%;
3D打印快速试制验证:某国产发动机厂商通过3D打印服务,3周完成6代叶片迭代,缩短研发周期70%。